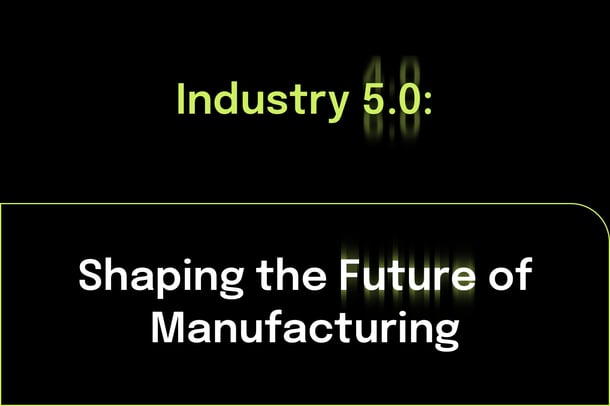
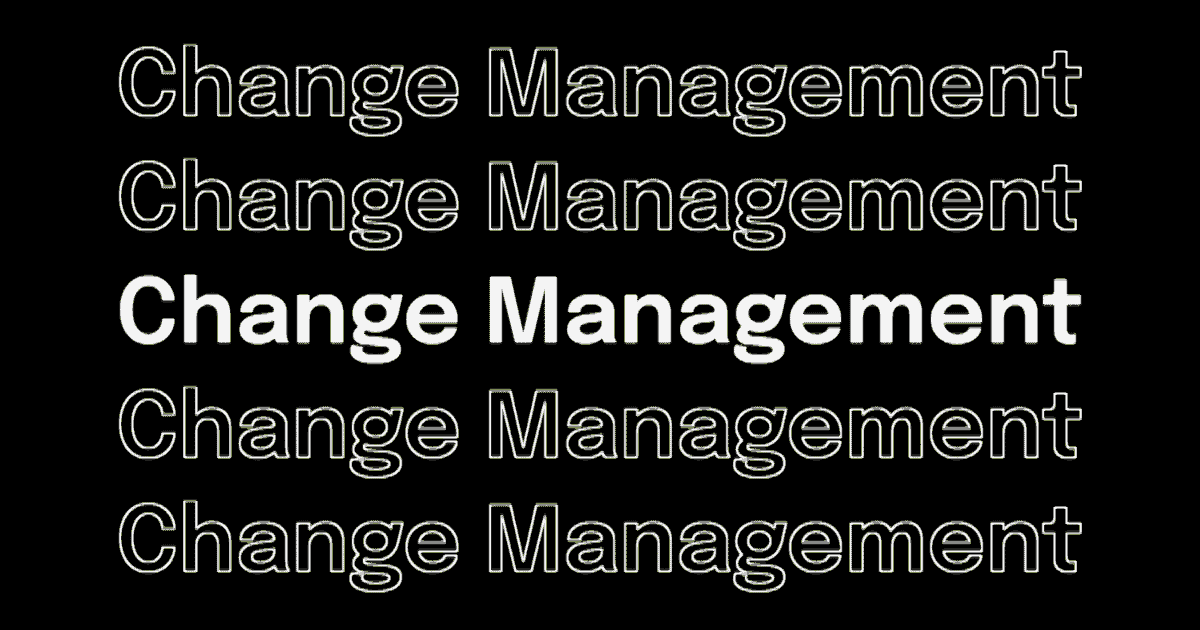
Change management in manufacturing: Best Practices and Strategies.
Change management techniques in manufacturing allow us to implement change at scale. They provide a stable framework assess, improve, revise and iterate on successful initiatives from the shop floor to the C-Suite.
What is change management?
Change management describes the collective strategies and techniques that a company uses to deal with new things, experiences, or conditions.
This could be an economic downturn, increased demand, tighter profit margins, new leadership, a merger or acquisition, or most recently - the COVID-19 pandemic.
Change management gives us a stable, predictable, and repeatable framework to deal with new things at scale - whether that’s introducing new tooling on a production line, implementing new software, or coping with a global crisis.
Change management has been around (formally) since the mid-19th century. Why do we need to continuously improve our change management strategies?
Because change is widespread and difficult.
- The typical organization today has undertaken five major firmwide changes in the past three years.
- Nearly 75% expect to multiply the types of major change initiatives they will undertake in the next three years.
- Half of change initiatives fail, and only 34% are a clear success
Source: Gartner
Couple these facts with the rapidly changing technological and human components of the manufacturing industry, and it's clear that new strategies are needed to keep pace.
Change management in manufacturing.
In this industry, change and iteration are a fundamental and routine part of success.
Anyone who's spent enough time in the industry is familiar with popular lean and continuous improvement philosophies like Lean and Kaizen.
Sound familiar?
Yup, that's change management.
These are familiar examples of change management processes that deliver value to the entire manufacturing value chain.
Not only is change management a critical component of familiar continuous improvement initiatives, it’s also essential for dealing with:
- Organizational change: Changes to leadership, corporate structure, or established hierarchies.
- Workflow change: Changes to processes, procedures, and 'ways of getting it done.'
- Technological change: Changes to the tools, equipment, and resources used to carry out manufacturing processes and to make these processes more efficient.
Often, the success of manufacturing initiatives hinge on iteration and flexibility. These processes deliver both in a scalable, measurable format.
Navigating digitization with change management.
Technological change.
The advancement of manufacturing tech demands a prioriotization of change management initiatives.
For the better part of a century, these strategies have been used to guide organizations through periods of technological change and ensure that these new elements are implemented successfully at scale.
If not managed correctly, today's paradigm-shifting technology can add confusion to a manufacturing workflow. Change management processes allow manufacturers to cope with the initial disruption of new technology, and ensure that organizations are implementing them into their workflows in a stable, scalable, and consistent manner. They deliver the framework to evaluate
This can be anything from:
- AR and VR tools
- Digital work instructions and SOPs
- Data analytics and BI tools
- MES and ERP solutions
- Digital skills platforms
Regardless of the tech, the process is more or less the same. Change management strategies provide an iterative framework to hypothesize, implement, evaluate, and iterate.
Leveraging digitalization.
The exciting part about today’s digital landscape is that technological advancements on the shop floor are not just something to be coped with or managed - they can actually make the change management process more effective.
💡Example: Lean methodologies like Plan Do Check Act (PDCA) hinge on communication, evaluation, and standardization. If you pair a framework like PDCA with a frontline knowledge management software, the benefits are immediately clear:
Communication: Frontline workers can deliver real-time feedback about the viability of a new process in the flow of work, and can offer potential improvements to be reviewed.
Evaluation: Usage, effectiveness, feedback, and other data can be stored, viewed, and evaluated in a central platform. Data updates instantly, and projects can move forward independent of scale.
Standardization: Implementing change hinges on standardization. With digital tools, new processes can be standardized in SOPs and work instructions, rolled out at scale instantaneously.
Frameworks for change management in manufacturing.
There are a number of established and proven models for enacting change.
- Lean Change Management
- Kurt Lewin's 3-Step Change Model
- John Kotter's 8-Step Process for Leading Change
- Change Management Foundation and Model
- The Prosci ADKAR Model
- The Plan-Do-Check-Act Cycle
- And many more!
Plan-Do-Check-Act: A familiar example.
If you’ve spent time in the manufacturing space, you’ve probably heard of the Plan-Do-Check-Act (or PDCA) methodology.
If you haven't, it's a great representation of a common Lean method for enacting, scalable, measurable, meaningful changes in manufacturing initiatives.
This is a simple, structured approach to executing effective change management in manufacturing processes.
Change management Do’s and Don’ts.
DO
- Define goals
- Monitor risk and assumptions
- Communicate effectively
- Deliver effective training
- Monitor success and make changes where necessary
DON'T
- Create a solution before you fully understand the problem
- Forget to prioritize communication
- Fail to validate your solution before implementing
- Implement change without buy-in (from the shop floor to the C-Suite)
- Be afraid to fail and iterate
Author
Revisions
It's time to simplify frontline training
Work instructions, checklists, and skills management - all in SwipeGuide
- Cut training time by 50%
- SOC I and II compliant
Get to know us
SCHEDULE YOUR DEMOResources
-
1
How to empower your frontline with better instructional design. -
2
How to gain the edge in Industry 4.0 with smart manufacturing practices. -
3
How to make excellent digital work instructions. -
4
How to deliver continuous improvement at the frontline with Lean principles. -
5
How to capture, share, and improve expert knowledge with digital SOPs.