The coronavirus pandemic was one of the biggest disruptions in recent history to supply chains, staffing, and demand. Across the world, manufacturers were rising to the challenge to keep their employees and their communities safe and healthy.
They did this in different ways, but they had one thing in common: flexibility.
Flexibility in manufacturing =
Flexible manufacturing allows the organization to quickly react to predicted and unpredicted changes. This can include a change in supply, demand, or price, but also creating new processes and procedures or reinvent old ones for a group of constantly changing employees.
Let's look at some examples from the leading manufacturing companies on how they adapted and continuously improved to change during COVID.
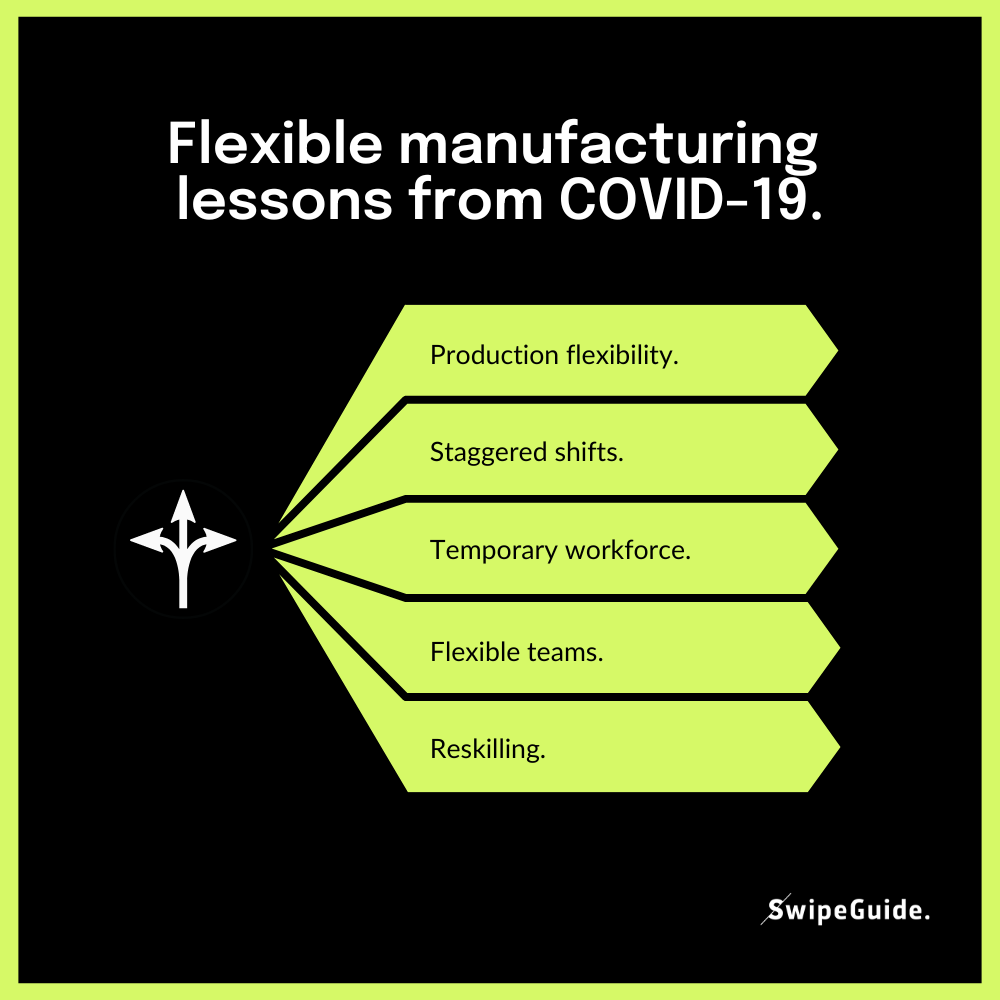
1. Production flexibility.
Ramping up production and converting new production lines to produce products that are needed and in-demand at the moment.
2. Staggered shifts.
During COVID, factories staggered shifts on the shop floor to help compensate for higher-than-normal absences. Simultaneously, workers are being separated and required to keep a distance of at least 1.5 meters from their colleagues.
3. Temporary workforce.
Hiring a temporary ad-hoc workforce for a period of time might be a good idea to help manage overstressed tasks in the short term. This helps address the additional workload caused by absences and higher demand for certain products.
4. Flexible teams.
Due to the fear of recession, many companies might have to work through the aftermath of the crisis with flexible workers and a reduced headcount in order to keep their factories humming. Make sure processes are standardized and capabilities transferable.
5. Reskilling & redeployment of existing employees.
Many companies are reskilling and upskilling their existing workforce to perform new or different tasks within the company, outside of their normal duties. These people already know how the facilities work and don’t need to be taught the basics.
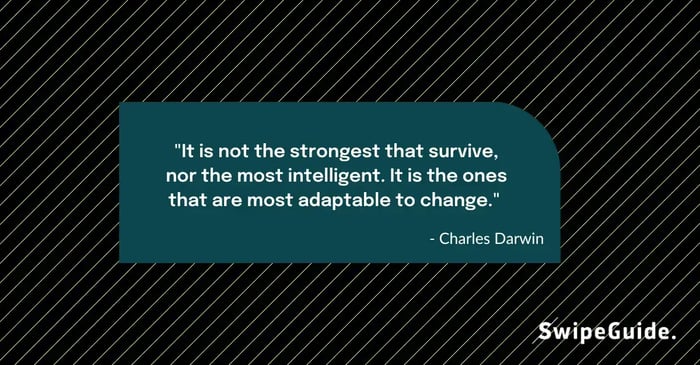
Want to learn more about how manufacturing teams can be more efficient?
👉 Reduce Human Error in Manufacturing = Improve Product Quality.
👉 Crowdsourced Knowledge Drives Continuous Improvement.
👉 How to continuously improve processes.
[Updated in March 2023]