What causes errors in manufacturing?
1 in 4 times when unplanned downtime happens in manufacturing, it's caused by human errors.
Some TPM and lean manufacturing experts claim that 85-99.9% of product quality related issues in manufacturing is caused by humans.
But why do these errors happen?
The top 10 causes of human errors in manufacturing are: 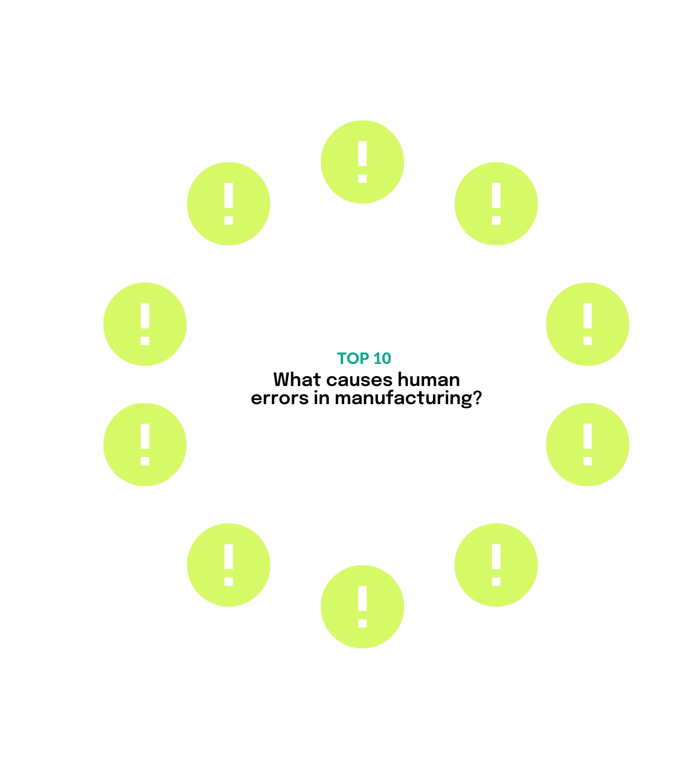
Even though it's easy to blame humans for causing errors, please avoid it.
The REAL reason usually lies much deeper.
Two noteworthy root causes worth giving some extra attention to:
training and stress.
1. Lack of training.
The Association for Manufacturing Excellence finds that the average American manufacturing company has an employee turnover rate of around 37%. This is a huge figure.
According to The Manufacturing Institute, 97% of manufacturers worry about critical operational knowledge disappearing from their organization when employees leave.
That's why manufacturing organizations should focus more on frontline training. Not only when onboarding newcomers, but throughout their tenure at the company through continuous on-the-job training that's easy and accessible for everyone.
2. Stress.
Not very surprising, but stress causes errors.
48.8% of human error in manufacturing can be explained by a stressful work environment. Underlying reasons include:
- Pressure from "doing more with less"
- A "punishing culture" where mistakes are seen as evil, instead of a "learning culture" where continuous improvement is encouraged.
- Demotivating and repetitive tasks that lead to fatigue.
- Demanding managers that lack proper leadership training.
Stress and lack of proper training are two major causes of human error in manufacturing.
Preventing human errors.
Where should you start?
Well, preventing human errors starts with understanding and developing the capabilities of the human aspect of your operations.
Of course, there’s no single, simple answer to this problem. Rather, it’s the intersection of a number of elements and solutions working together across your operations. .png?width=774&height=851&name=reduce%20human%20error%20(4).png)
1. Prevent the flow of errors.
To prevent errors, you need to understand them first.
This happens on the shop floor, when supervisors physically observe the habits and potential problem areas within a process. From here, they can begin to create productive and supportive systems of management to address the areas in which they’re lacking.
Gemba walks are an excellent example of this technique and they can be supported by tools such as digital checklists.
2. Train best practice.
Employees need to know how to complete their work according to the standards defined for your processes.
Digital work instructions and SOPs are a great place to start since they deliver accurate and optimized knowledge directly to workers in the moment of need.
3. Implement 5S.
5S and similar methods are proven strategies that create a visual workspace where any deviations are immediately recognizeable.
5S stands for: Sort, Set in Order, Shine, Standardize, and Sustain.
Combined with the above techniques, this gives frontline workers the tools they need to embrace accountability as they complete their daily tasks at the line.
4. Devise systems to learn from mistakes.
Mistakes are inevitable on the shop floor.
But when they happen, we need to learn from them. It’s up to supervisors to implement optimized systems that can identify and then correct the root cause of the error.
5. Automate repetitive processes.
If a process can be automated in a cost-effective way, do it!
This is a great way to cut out the possibility of human errors and also save time for workers and supervisors alike.
Knowledge + continuous improvement.
Digital solutions make it easy for teams to succeed.
They’re given the knowledge and resources in a format that makes sense and removes many of the traditional blockers that cause human errors in manufacturing:
- Work instructions and standards being out of date.
- A lack of clarity and usability in standards.
But there’s another element to understanding and preventing human errors:
How do we make sure that our workforce is actually adhering to the standards we deliver?
Just like in the steps above, this starts on the shop floor with a dialogue about the work being performed. The same Gemba walks that help diagnose problems can also be used to monitor adherence to standards by connecting supervisors and frontline workers throughout their daily work
Remember, removing human errors is a process.
These improvements won’t happen overnight, or as the result of a single sweeping initiative. Rather, it’s about embracing tools and processes that facilitate the continuous improvement of your processes and procedures and promote frontline excellence on the shop floor.
Learn more about reducing errors in manufacturing:
👉 Crowdsourced Knowledge Drives Continuous Improvement on the Shop Floor.
👉 Digital Kaizen SOPs to Standardize and Continuously Improve.
👉 Webinar: How to Ensure the Highest Product Quality by Avoiding Human Error.
Contributor 📝
This article has been written in collaboration with Mark van Bokhoven. Mark is a specialist in Lean, TPM, and OpEx strategies and focuses on sustainable improvement in customer-oriented companies, including Refresco and Heineken. He's also an author and has published a number of books on continuous improvement and management strategies.