Standard Operating Procedure =
- Documents (either digital or physical) that provide standard guidelines for your team members to complete a given process according to proven best practices.
- SOPs are often used to ensure that operations run smoothly, with cohesion and performance uniformity.
- SOPs also ensure compliance with safety measures and regulations.
Example:
- You work at a large beer brewer. You’re tasked with reducing quality variations in your products and ensuring safety on the shop floor.
- Beer brewing entails many different processes with specific steps and recipes. If you follow different procedures every time, your results will be different and the recipes will be hard to replicate. This means your product’s quality and brand will suffer.
- To prevent this, you develop SOPs to ensure your brewing procedures are less error-prone and consistent. Because team members follow a standard procedure, everything is measurable. Your quality team can analyze whether the steps taken during the brewing process achieved the desired results. They can also identify improvement areas more easily.
- Besides contributing to quality assurance, SOPs are useful for effective resource management. Fewer errors result in fewer product losses, and therefore lower costs.
- SOPs also facilitate knowledge transfer. This is especially relevant for organizations with high rates of employee turnover, or situations where employees are reaching retirement age. Standard operating procedures document how processes should be performed; meaning knowledge is not exclusive to an individual employee but captured company-wide. This, in turn, makes it easy to train and onboard new employees.
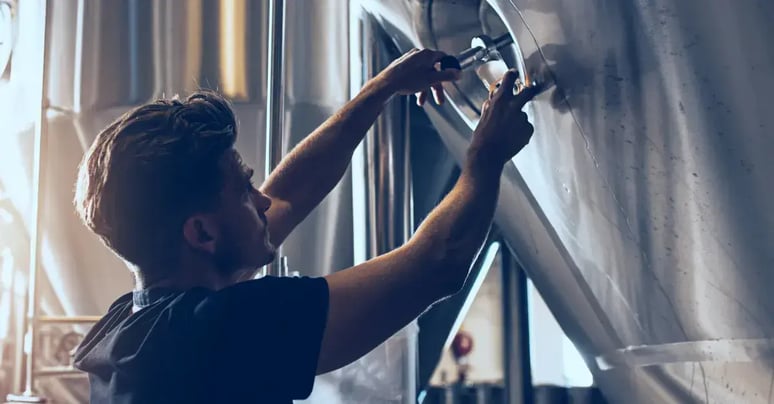
SOPs tell how to perform tasks according to standard and help with consistency, safety, and compliance.
Work instructions vs SOPs: how are they different?
What makes SOPs different from work instructions?
SOPs are generally high-level documents, but sometimes they can be instructions in themselves. The difference between work instructions and SOPs is mainly the level of detail.
Here’s a handy way to think about it.
Organizational processes are typically broken down into:
.png?width=280&name=Process%20(4).png)
1. The process:
A set of related or interacting activities, which transform inputs into outputs.
= the overview of all pieces related to each other that transform into a finished puzzle.
.png?width=279&name=Process%20(3).png)
2. The standard operating procedure:
A process that happens in a specific way, including specifications on how it happens.
= the guidelines on how to solve the puzzle.
.png?width=280&height=187&name=Work%20instruction%20(2).png)
3. The work instructions:
The best way to complete a specific procedure that allows anyone to complete a task.
= individual actions of placing puzzle bits on the right spots in order to solve the puzzle.
When should I break down the SOP?
When a procedure consists of multiple tasks, you may want to break that down into individual instructions. When deciding whether you need to break down your SOP into individual instructions, consider the following:
- Is the desired outcome to inform employees about a certain standard or do I want to teach people how to do something?
- Should the procedure be broken down into smaller steps/tasks to make it understandable?
- Do I need to provide more information or troubleshooting details per step?
- Do I need to provide visual instructions?
Structure of a SOP.
When SOPs are broken down into individual instructions, we recommend the following structure:
- Guide: Imagine this as the full “product manual” for your SOP. It’s a high-level document that contains every topic, instruction, and step to effectively complete a set of different tasks in a factory or with a certain machine.
- Topics: your Guide can be divided into topics, categories or themes. For example, all procedures for cleaning machines in your factory can be collected under the topic "Cleaning."
- Instructions: each topic or category will have its own set of instructions. These are a specific set of steps to perform a task. For example, under “Cleaning” you will have specific instructions to wipe or wash different types of machines.
- Steps: these are single actions within an instruction. They should be focused and specific. The steps within a particular instruction always focus on the same goal: progressing from an initial to the desired state.
-1.png?width=700&height=532&name=how%20to%20write%20an%20instruction%20manual%20(1)-1.png)
But what about checklists?
As an alternative to instructions, you can use checklists in your SOPs. Checklists enable you to capture more operational data on the factory floor or in the field and gather input from users.
Checklists are especially great for:
- Safety, quality, cleaning, and 5S.
- Go-sees, inspections, audits, and Gemba Walks.
- Machine startup and shutdown procedures.
- Maintenance support.
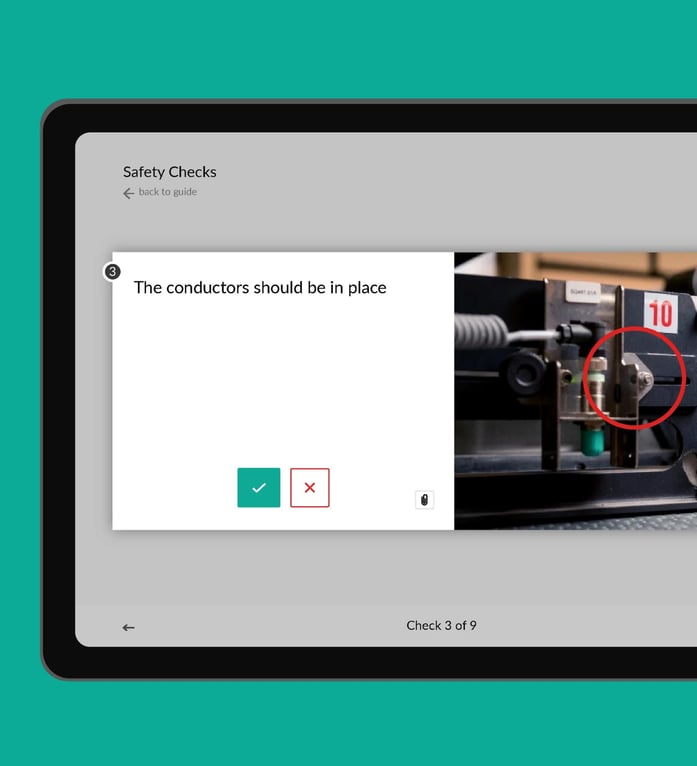
Checklists can be a great addition to your SOPs.
Let's recap: what is a SOP?
- Standard operating procedures are documents (either digital or physical) that map out how to perform tasks.
- SOPs help you guarantee quality, repeatability, efficiency, and skills transfer.
- The type of SOP you choose should vary depending on the complexity of the process.
- Dividing your SOP into action-oriented instructions or checklists is useful when you’re dealing with a complex process and you want to teach employees how to execute individual tasks or actions.
Read more about SOPs:
👉 Standard Operating Procedures: 5 Reasons Why You Need Them.
👉 Standard Operating Procedures: Best Practices & Guidelines.
👉 Benefits of standardizing operating procedures.