Waste?
We bet that you've dedicated a lot of your time to learning about - and trying to eliminate - manufacturing waste.
Waste in lean manufacturing =
anything that doesn't add value to the product (or customer).
But waste isn't always obvious. Sure, things like employees lounging by machines or throwing away good materials obviously cost your business money, time, and product quality.
Effective lean manufacturing aims to identify the subtle and far-reaching waste factors that creep into your lean manufacturing processes and cost you in the long run.
The 7 types of waste in lean manufacturing.
There are seven key areas of waste factored into lean manufacturing, as originally identified by Kaizen master Taiichi Ohno are:
1. Transport
2. Inventory
3. Motion
4. Waiting
5. Overproduction
6. Overprocessing
7. Defects
We’ve gathered them all in an infographic below (click to enlarge!):
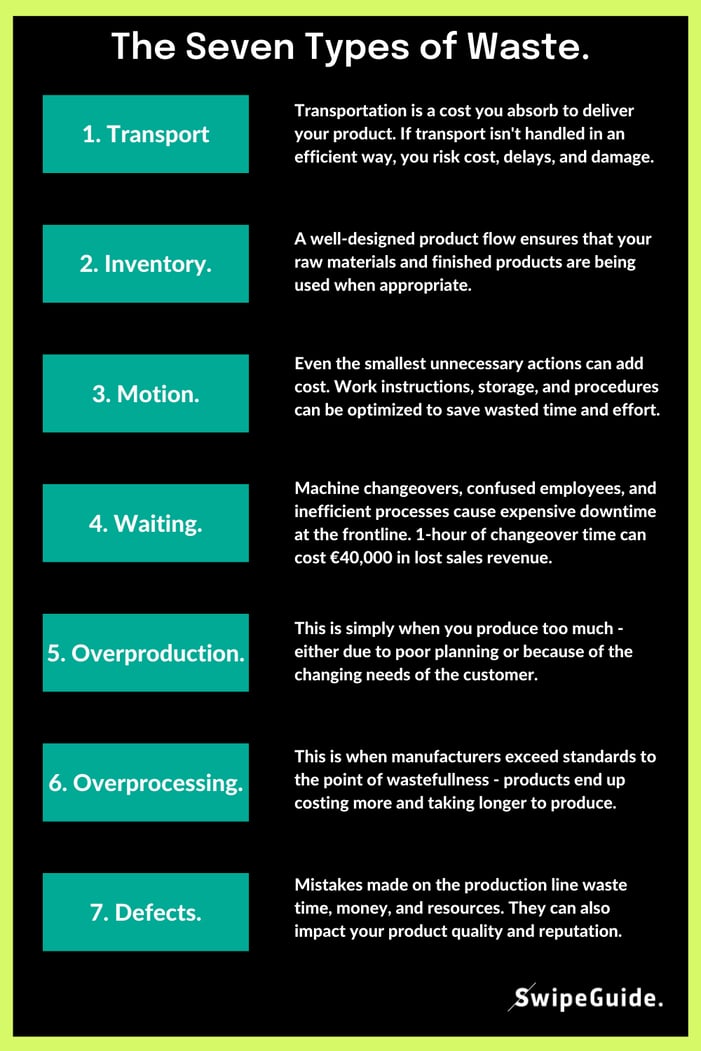
Make waste a part of the past.
The factory floor is changing fast. Industry 4.0 is revolutionizing the factory floor and processes are only becoming faster and more complex. Modern workers simply need better, faster, and smarter solutions for process management and training.
Waste reduction is the soul of lean manufacturing. To truly enact a cycle of continuous improvement in our modern era, businesses need to provide their shop floors with comprehensive digital tools that can keep pace with the factories of the future
Want to learn more?
👉 Learn Lean philosophies: What is Takt Time in manufacturing?
👉 Best devices for the frontline - our device recommendations.
👉 Improving standard work for Heineken: Read the Customer Story.
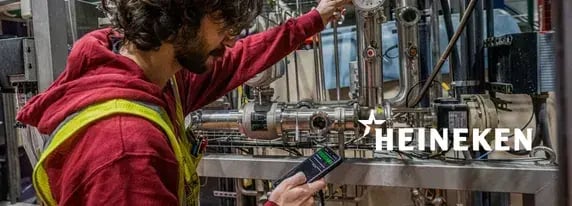