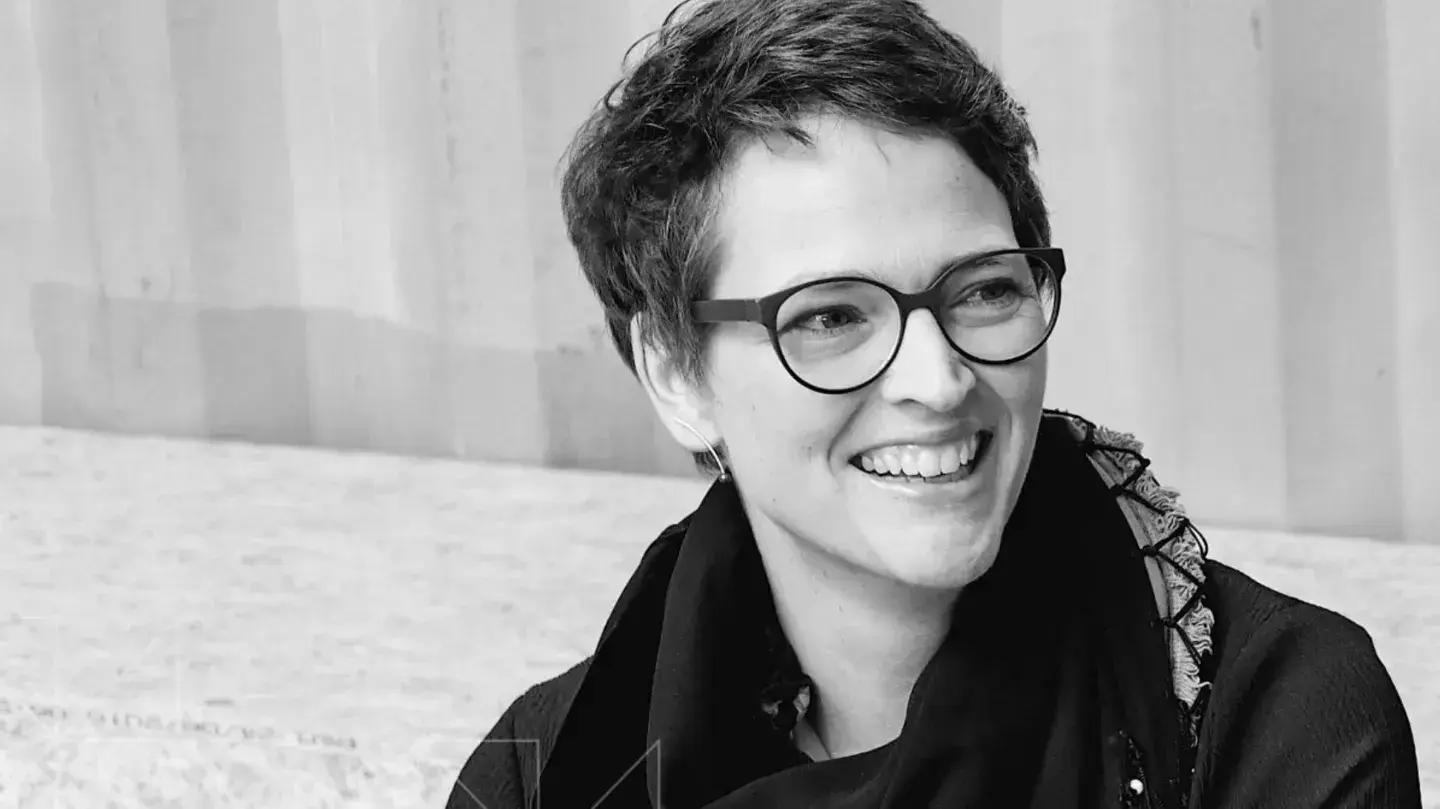
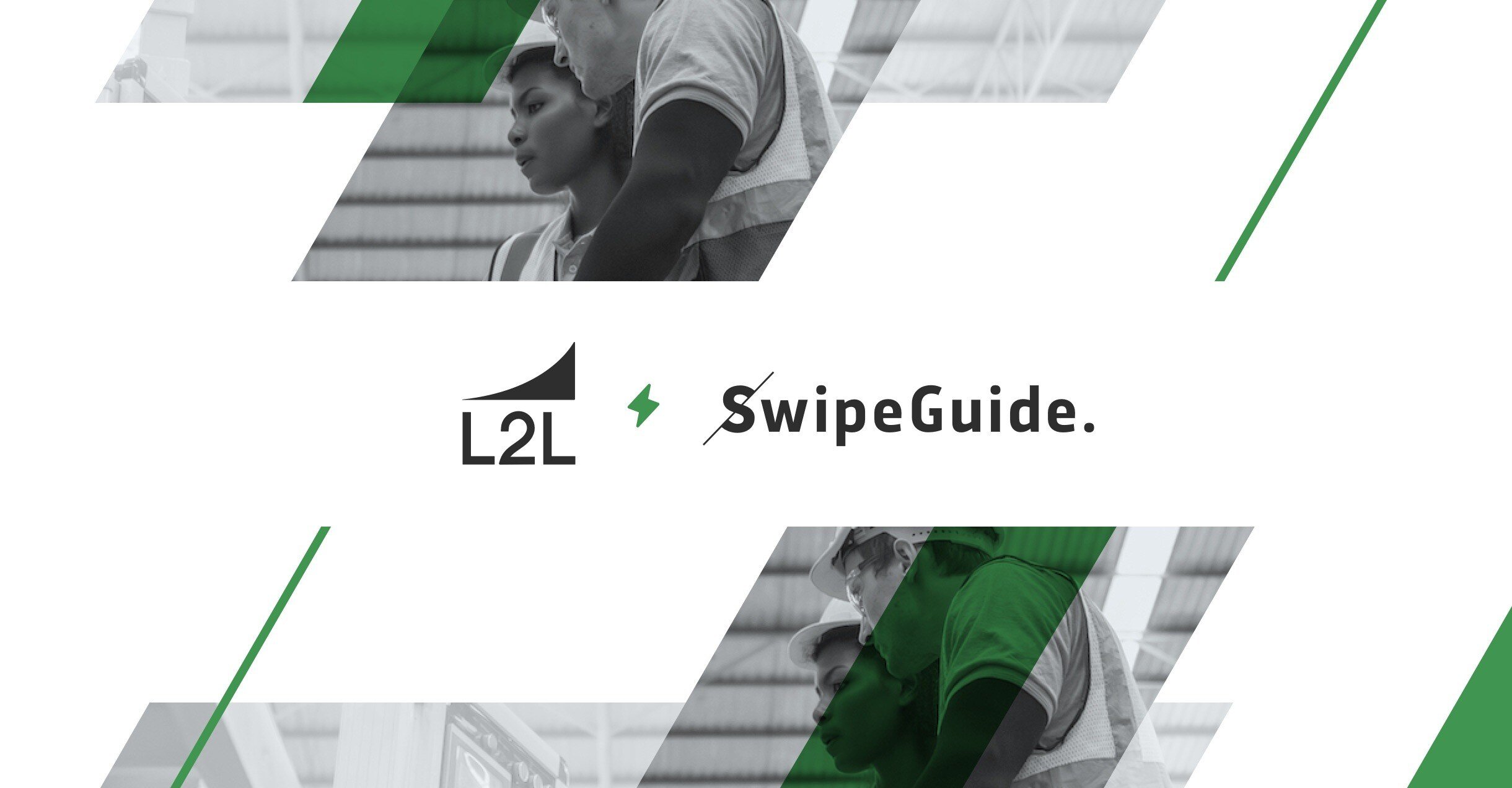
SwipeGuide Joins Forces with L2L to Power the Connected Workforce
Say hello to the future of the connected workforce - SwipeGuide has been acquired and is now part of the L2L Connected Workforce ecosystem! This allows us to expand beyond standardization and training to streamline the full spectrum of manufacturing operations. Expect a game-changing solution built for the frontline that drives end-to-end manufacturing performance at scale.
SwipeGuide joins L2L to make a bigger impact.
SwipeGuide's CEO and founder Willemijn Schneyder about the acquisition
We founded SwipeGuide with a clear mission:
to simplify the way people work and learn at the frontline.
This message has formed the core of our product since the beginning.
We’re incredibly proud to have demonstrated a different path to digital transformation by involving everyone at the frontline and on the shop floor.
Our clear-cut and collaborative work instructions enable continuous improvement and help digitize the decades of expert knowledge amassed by a senior (and quickly retiring) frontline workforce.
From there, we tackled skills. It’s no secret that skills gaps and turnover are plaguing the industry. There’s a critical and growing disconnect between our human workforce, the task at hand, and the skills they need to do the job.
SwipeGuide customers see the headaches and bottlenecks caused by paper-based resources and outdated skills management evaporate before their eyes. To tackle this challenge, we have fundamentally and scalably transformed how the frontline workforce captures knowledge, standardizes work procedures, shares best practices, and develops essential skills.
All of this because we know that the frontline workforce - this incredible group of people that powers the manufacturing industry - is the key to sustainable production patterns and ultimately the foundation for producing a fantastic end product.
We focus on the frontline in an age where they’re still critically underserved.
SwipeGuide was created because of this frontline paradox. Our modern manufacturing industry depends on the success of the frontline, and yet the frontline workforce is still given tools and training from the 20th century.
In 2024, there is still a clear and urgent need for manufacturers to have more resources for frontline teams. Organizations need an end-to-end solution to connect their real-time performance with the benefits of improved standardization and training.
Users from the shop floor to the C-suite need resources that provide visibility and drive action - resources beyond what SwipeGuide can deliver alone.
Enter L2L - the first connected workforce platform, founded in Salt Lake City in 2010.
Together, SwipeGuide and L2L represent a joint response to the growing needs of the frontline.
L2L provides manufacturing companies around the world with a real-time view of what is happening, where it’s happening, and why. It can plan work, schedule workflows, assign tasks, and track performance. The company has made a name for itself as the first true connected workforce platform with a rich history of empowering workers to manufacture better together.
In terms of ROI, L2L customers have seen an average of 30% increase in employee engagement and a 20% reduction in unplanned downtime while eliminating disruptions.
This is what L2L does.
SwipeGuide customers will soon enjoy an expanded product offering including the capabilities provided by the L2L Connected Workforce Platform. L2L empowers every member of the frontline team to solve problems together - fast.
With real-time visibility into production and maintenance status, seamless collaboration, and the ability to automate action, L2L helps teams boost performance, improve availability, and optimize quality.
At the core of the L2L Platform is Dispatch, a connected worker hub that empowers workers to improve performance task management, dispatching, and tracking that provides a digital record of all events to diagnose root cause issues.
1. Increase availability and machine uptime.
Unplanned downtime not only hurts productivity, but it also demoralizes teams. By enlisting every member of the frontline team to participate in preventative maintenance and by automating predictive maintenance, L2L improves equipment availability and reduces downtime.
Real-time alerts and automated actions enabling condition-based and predictive maintenance, streamlined spare parts management, and optimized asset utilization all allow manufacturers to improve availability and performance.
2. Improve performance and output.
Driving improved performance requires a focus on continuous improvement and a team effort towards a common goal. L2L delivers shared visibility into key production metrics for the entire frontline team, enabling frontline employees to work together better and take the right actions to optimize performance.
L2L’s manufacturing intelligence capabilities (including artificial intelligence (AI), business intelligence (BI), and automated intelligence) automate routine tasks, deliver alerts, and provide recommendations to address production issues, allowing teams to diagnose and solve root-cause issues before they become major problems.
L2L helps teams achieve more together with key features like:
- OEE measurement
- Product order management
- Scheduling
- Key metric monitoring
- Changeover management
- Material handling
By supporting the entire frontline team with real-time insights and automation, L2L helps manufacturers streamline workflows, improve communication, and identify and address production issues, improving overall manufacturing performance.
3. Ensure quality.
A holistic approach to quality engages the entire frontline - not just inspectors. By digitizing key quality principles like 5S and enabling layered process audits, L2L identifies and addresses quality issues faster, reducing scrap and rework.
Key features include:
- Issue and material containment
- Quality checks and alerts
- Rework and scrap management
- PCQI compliance
- Material inspection
Each of these helps ensure product quality while reducing defects and meeting regulatory standards.
How does SwipeGuide fit in the picture?
We’re excited to build out the future of the connected workforce by combining our frontline training solution with the L2L platform. This strategic partnership allows us to expand beyond standardization and training to streamline the full spectrum of manufacturing operations.
Integrating with the L2L ecosystem means that we can jointly empower frontlines to profitably meet the ever-growing global demands. From retaining top talent and enhancing product quality through frontline development tools to improving operational efficiency.
What happens now?
Together, L2L and SwipeGuide will continue to deliver on our shared commitment to improving manufacturing performance and supporting frontline teams with effective, scalable, and user-centric connected workforce tools. As a team, we’re creating a future where manufacturing work is more efficient, more fulfilling, and more sustainable for everyone in the long term.
SwipeGuide will continue to operate as we have always done. You can count on our continued support, customer service, and dedication from the team to our customers. Our customers will continue to have full access to the SwipeGuide platform, frontline apps, and all current services without any interruptions. In fact, you can expect even more from us over time, including improved features, new innovative products, improved service coverage, and a more integrated user experience.
For more details on how L2L and SwipeGuide work together visit l2l.com/swipeguide
Are you a customer and want to learn more about what this means for you?
Book a call with one of our customer success managers!
Author
Revisions
It's time to simplify frontline training
Work instructions, checklists, and skills management - all in SwipeGuide
- Cut training time by 50%
- SOC I and II compliant