Manufacturers in 2023 are struggling big time. One of their biggest issues is what experts are calling "brain drain."
Not only is there a global supply chain uncertainty, but the cost of running operations is extremely high, and also - there’s a lack of skilled people.
(See an explanation of each step at the end of the article)
“What is the most pressing issue in manufacturing atm?”
After interviewing dozens of manufacturing leaders in the past few weeks, I've concluded that there’s one common nominator in every conversation, no matter of industry or location.
→ That’s the skills and labor shortage problem.
Skills shortages are caused largely by the retiring generation of frontline workers. I like calling this phenomenon the “grey tsunami”. But also younger frontline workers leaving for other jobs.
Actually, a whopping 63% of Gen Z frontliners want to leave their current job. Reasons being (according to Arlington Research):
-
Feeling burned out at work (58%)
-
Lack of appreciation (53%)
-
Lack of motivation and engagement (52%)
-
Poor compensation (52%).
It’s interesting to see that it’s not all about the money - people want to feel appreciated and engaged in their jobs, without being overworked. Which is pretty logical.
-png.png?width=774&height=310&name=FTR%202%20(1000%20%C3%97%20400%20px)-png.png)
Critical operational knowledge - lost forever.
97% of manufacturers worry about critical operational knowledge disappearing from their organization (according to The Manufacturing Institute) with leaving employees.
Of course, we all like to believe in this industry 4.0 fairytale. Digital transformation and smart manufacturing surely has all the answers.
However, the reality is that only 26% of all digitalization use cases in manufacturing were scaled beyond a pilot last year.
Mainly due to complexity, lack of people, and low adoption rate among frontline teams.
A very unpredictable storm.
As one senior director at a leading food and beverage company described it:
"The current market is like an unpredictable storm."
Pretty accurate.
Nobody knows what’s gonna happen with the current market.
The thing we DO know, however, is that production efficiency still depends very heavily on people.
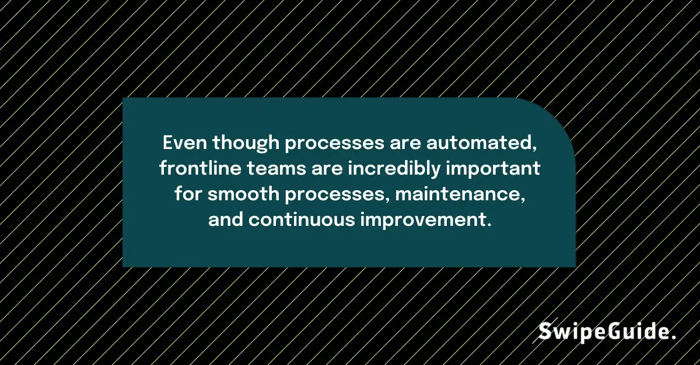
So how can we solve the brain drain and labor problem now, without waiting for 6, 12 or 24 months for this unpredictable storm to calm down?
5-step process to stop the brain drain:
- Audit your procedures. First, focus on what we can do instead of staring blindly at the uncertainties. Start with focusing on your processes and procedures. Are they standardized, documented, and up-to-date?
- Capture knowledge. Then, make sure to continuously capture the critical operational knowledge from your frontline team members (before they leave).
- Involve to motivate. Research shows that if people are involved in the shaping of processes, they feel much more engaged and motivated in their jobs. Retain and motivate your team members by empowering them to take ownership of your standard operating procedures and work instructions.
- Inform. Standardized procedures are pointless if nobody is aware of their existence. Share and communicate your best practices so that the right people have easy access to them whenever they need them.
- Continuously improve. Future-proof your processes by regularly auditing your procedures. Do this by collecting feedback and improvement ideas from your frontline experts and implementing lean philosophies like Kaizen.
Learn more about frontline training and how to stop manufacturing brain drain:
👉 Smooth frontline training programs.
👉 Gain the Benefits of TPM Manufacturing with Frontline Knowledge.
👉 Crowdsourced Knowledge Drives Continuous Improvement on the Shop Floor.
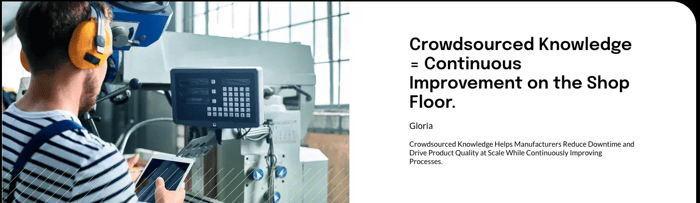