When talking about continuous improvement in factory operations, there's a gazillion different ways to identify problems and improve processes.
In this short TPM summary article, we'll look at OEE improvement in factory operations based on identifying losses, standardizing processes, and continuously improving them.
In an overly simplified world this is how it goes:
1️⃣ Define the losses.
2️⃣ Make a loss tree.
3️⃣ Sort the losses.
4️⃣ Define problems.
5️⃣ Find the root cause.
6️⃣ Improve the process.
Before we dive into the details of this, let's work through some definitions.
What is a loss?
In manufacturing, there are more than 20 types of losses. However, TPM people typically talk about 4 groups of losses:
01. The 6 major losses* (see visual below)
02. Machine reliability: shut-down losses.
03. Man losses: human efficiency
a. Management loss: eg. no instructions.
b. Operating motion: eg. incorrect procedures.
c. Line org: eg. layout & Logistics eg. supply.
d. Measurement: eg. quality monitoring loss.
04. Resource use efficiency: eg. yield and energy.
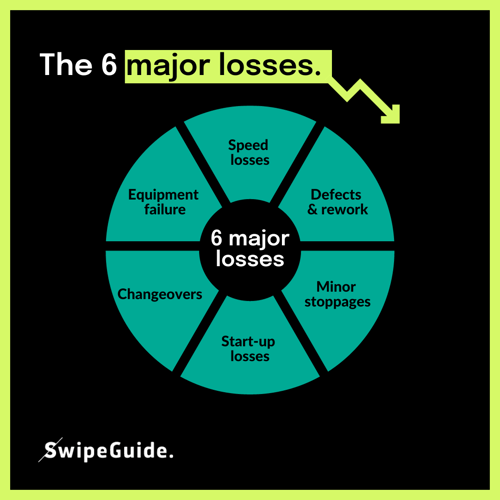
What is a loss tree?
A loss tree is basically a list of losses in a factory. Teams usually report on eg. time, percentages, and capacity loss and present the loss tree in a bar chart format.
Here's an example showing time loss in hours:
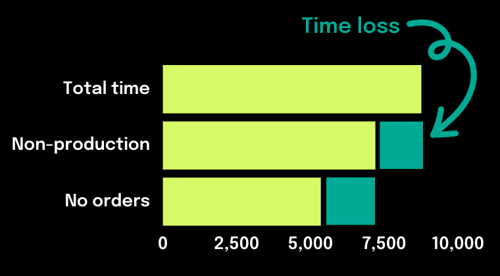
When you report on these losses and the KPIs tied to them, this is usually what's recommended:
01. Productivity: eg. equipment losses.
02. Quality: eg. rework and defects.
03. Cost: eg. raw material waste.
04. Delivery: eg. logistics losses.
05. Safety: eg. accidents time loss.
06. Morale: eg. training.
07. Innovation: eg. improvement ideas.
What's loss deployment?
To improve equipment efficiency, we need to understand the causes of inefficiencies and prioritize improvement activities. A loss deployment cascade helps you set priorities for improvement activities.
We can use problem-solving tools like the Ishikawa diagram (4Ms) to identify and address the root causes of losses:

Time to solve problems!
Okay, now that you've identified the root causes of your loss problems, we can start solving them. One of the most widely known and used problem-solving models in lean manufacturing is the "PDCA" framework.
What's PDCA?
PDCA stands for plan-do-check-act and is a well-known continuous improvement framework.
The PDCA framework is used for defining problems, developing solutions, evaluating the progress, and standardizing processes in order to continuously improve performance: 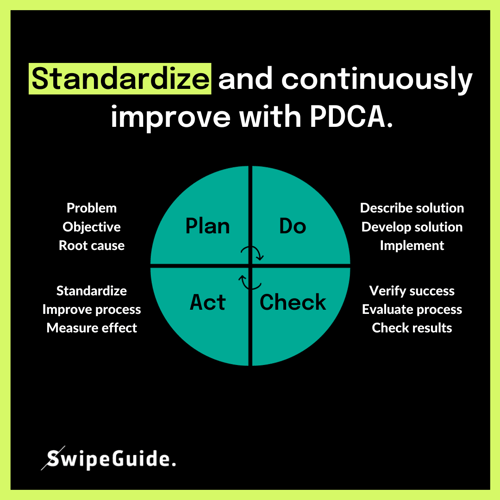
Continuous improvement never ends (as busy CI managers know very well) - that's why the PDCA framework is an eternal loop. When you've standardized the process, it's time to move back to the "plan" phase again and find new problems to solve.
The final summary.
Based on the walkthrough above, here's an overly simplified summary of what TPM teams can do to identify losses, standardize processes, and improve OEE in manufacturing operations:
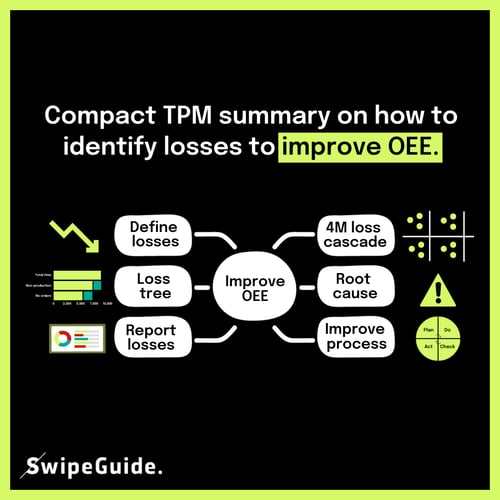
Wanna read more similar content?
👉 Aspiring Continuous Improvement Managers: Follow These 6 Tips
👉 What are Lean Principles?
👉 Digital Kaizen SOPs to Standardize and Continuously Improve.
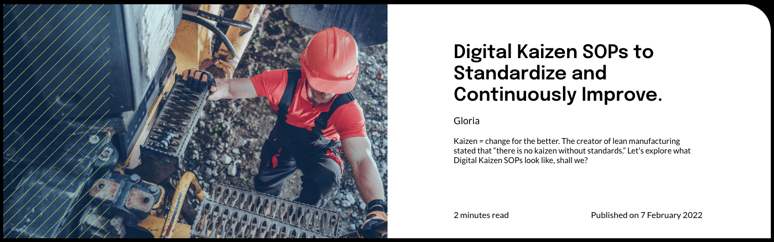