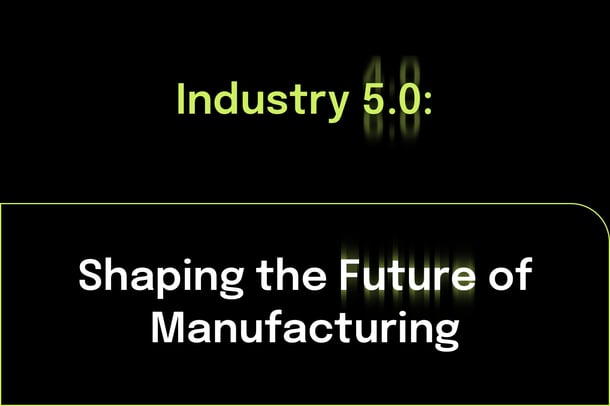
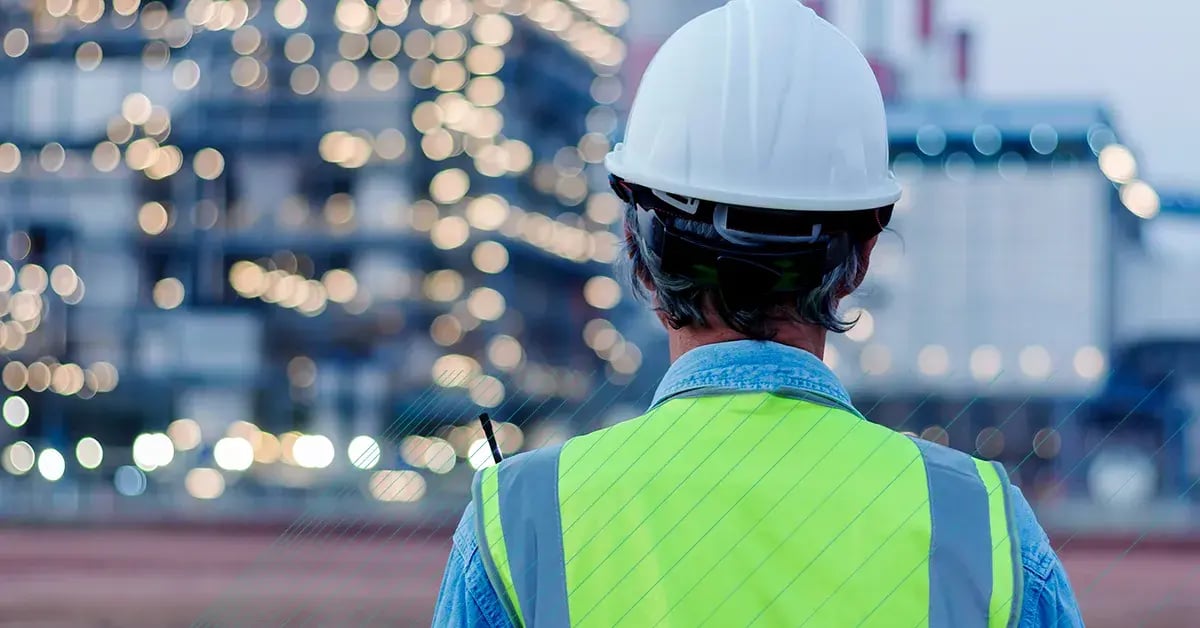
Want to Build the Factory of the Future? Focus on these 4 Areas.
Digital leadership, Tech-Augmented Workforce, Data-Driven Maintenance, and Zero-Touch Production are four of the cornerstone areas of building your Factory of the Future. Read more about these four key areas in this article.
Manufacturing has an unmatched potential to transform how we live.
We saw it during the industrial revolution, which led to large-scale changes like urbanization, an increase in wealth and innovation.
Today, we are seeing manufacturing take a large turn once more with industry 4.0. New technologies are emerging to make our factories more efficient and sustainable by reducing waste, optimizing energy use, and improving employee safety.
How is this new revolution taking shape?
Supply chain and operations leaders who are leading the change are focusing on these four key areas when building the factory of the future.
1. Digital leadership.
A leader is often measured by their ability to effect change. But as we all know, this isn’t easy. One of the biggest challenges supply chain, operations, and IT leaders face is convincing their team to adopt digital technology. They need to lay the groundwork for technology adoption with the board and the frontline.
One way to do this is by relentlessly pursuing a customer focus.
- For example, adopting collaborative work instruction software helps to reduce errors on the shop floor. We have seen that standardizing processes and digitizing instructions reduce production errors by 67%. This improves quality control and efficiency, which means you can reduce lead times and focus on delivering added value to your customers.
- Shifting your team’s time from firefighting and damage control to empowering value-generating activities will also help you drive adoption. Making the case for digitalization will be easier when you can show you can enhance your employee and customer experience.
- Another important goal is connecting all stakeholders to work for the same vision. According to a study conducted by SmarterChains about the CPG industry’s adoption of digital technologies, only 33% of the early plants have an enterprise-wide Industry 4.0 strategy in place.
2. Tech-Augmented Workforce.
A successful industry 4.0 framework will take the needs of all stakeholders into account. Leaders who are building the factories of the future are augmenting their workforce’s capabilities with digital tools.
These tools can include:
- Industrial tablets
- Smartphones
- Remote collaboration solutions
- Augmented reality solutions
- Artificial intelligence software that provides decision support.
The frontline in these factories is empowered to optimize workflows, share knowledge and data, and provide feedback to improve operations. Advanced plants widely use handheld devices such as smartphones or tablets on the shop floor focusing on data visualization, reporting, and auditing, while early plants are putting in serious effort to adopt them.
3. Data-Driven Maintenance.
Speaking of operations, maintenance is another area where digital leaders can add value with digital solutions in the factory of the future.
- Carrying out maintenance tasks is necessary. But do it too sporadically and you run the risk of disruptions, do it too frequently and you may be risking higher costs and inefficiency.
- Running predictive or prescriptive analytics on sensor data can help you determine the right maintenance schedule.
- You can also implement data collection and feedback systems for your frontline to assess when the next maintenance run makes sense.
4. Zero-Touch Production.
Zero-touch or automated production is seen as one of the ultimate goals of industry 4.0 and smart manufacturing. According to an Ericsson study, the average automation level in factories was 57% ten years ago. Today, it’s 69%. The figure is expected to be at 79% by 2031.
- To get to zero-touch production, digital transformation leaders are adopting a combination of solutions. One of them is the digital twin - a digital representation of products and production processes. Digital twins enable you to run simulations to pinpoint inefficiencies and implement improvements. Remote controlled-machines and collaborative robots are other technologies that you can use.
- Despite the potential opportunities offered by digital twins, even advanced plants lack the data readiness and expertise to define real-time models that can drive timely decisions, effective resource allocation and throughput optimization.
- These low-touch or zero-touch tools help you improve worker safety and streamline production processes. In all of these cases, it’s important to train and upskill employees for successful adoption.
- And remember: even if most production in the future factory is low or even zero-touch, it doesn't mean that the human frontline worker is made redundant. The heavy-lifting of repetitive and physical tasks is done by machines, with support from humans in tasks like service, maintenance, and quality control.
Read more about the factory of the future:
👉The Future is Bright for the Deskless Worker in Industry 4.0
👉The Future Factory. How to Future-Proof Your Operations
Collaboration 📝
This Factory of the Future blog post has been written in collaboration with SmarterChains.
Author
Revisions
It's time to simplify frontline training
Work instructions, checklists, and skills management - all in SwipeGuide
- Cut training time by 50%
- SOC I and II compliant
Get to know us
SCHEDULE YOUR DEMOResources
-
1
How to empower your frontline with better instructional design. -
2
How to gain the edge in Industry 4.0 with smart manufacturing practices. -
3
How to make excellent digital work instructions. -
4
How to deliver continuous improvement at the frontline with Lean principles. -
5
How to capture, share, and improve expert knowledge with digital SOPs.