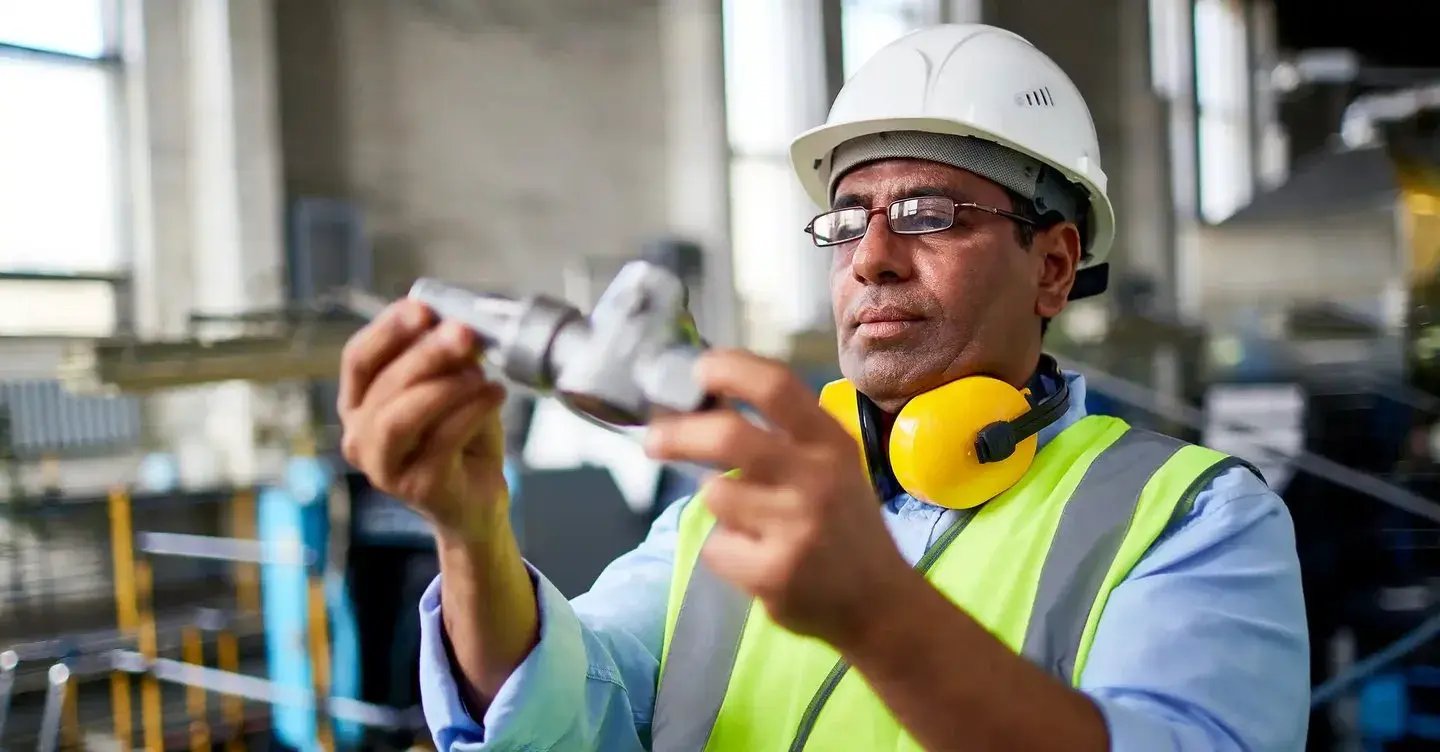
Manage product quality.
Prevent product recalls and errors caused by human mistakes with work instructions, checklists, and standard operating procedures.

Quality first.
Reduce unnecessary waste, recalls, and costs.
- Encourage a “quality first” mindset by involving frontline teams in improving processes.
- Dynamic work instructions engage frontline teams to challenge the status quo.
- Improve first-time-right by sharing best practices across the organization.
- Drive consistency and clarity.

“Quality first” mindset.
Encourage everyone to be sharp about detecting flaws - it’s not only the role of management or quality control.
READ MORE

Empower scalable first-time-right.
Everyone should have access to the most up-to-date work instructions in order to prevent errors from happening.
READ MORE

Standardize for consistency.
The goal of lean standard work is for everyone to follow the same steps in the same order to always achieve the same end result.
READ MORE

Leverage flexible tools.
Prioritize solutions that are flexible and easy to implement, up-to-date, and can be integrated with other SaaS solutions with stable APIs.
READ MORE

Don’t forget about safety.
Quality and safety walk hand in hand. Make sure that safety awareness is always top-of-mind by making it part of the day-to-day operations.
READ MORE
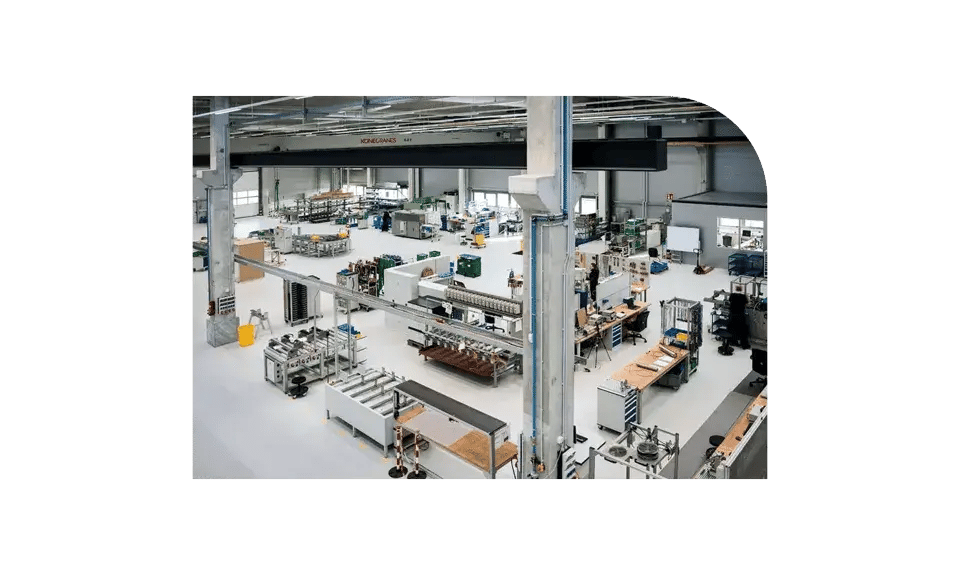
“Clear and accessible work instructions help us reduce quality variations in production.”
Plant Manager at Interroll
READ ALL CUSTOMER STORIESTake your processes to the next level.
SCHEDULE YOUR DEMOGet to know us
SCHEDULE YOUR DEMOResources
-
1
How to empower your frontline with better instructional design. -
2
How to gain the edge in Industry 4.0 with smart manufacturing practices. -
3
How to make excellent digital work instructions. -
4
How to deliver continuous improvement at the frontline with Lean principles. -
5
How to capture, share, and improve expert knowledge with digital SOPs.